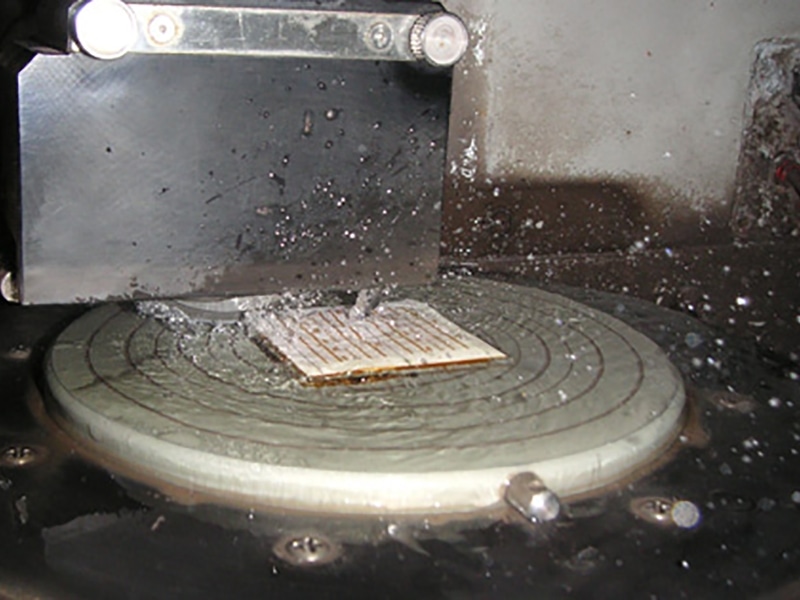
Wafer Dicing
Dicing is commonly used to separate optical components or electronics imaged onto wafers. The substrates can be waxed onto hard mounts to minimize chipping.
Experienced dicing experts are able to make precise cuts and grooves and optically align microscopic patterns.
What is Wafer Dicing?
The wafer dicing process separates small blocks of semiconducting material (known as dice) from a semiconductor wafer. Depending on the application’s needs, the dicing process may involve wafer scribing, through cutting, or wax mounting. The wafer is sawed in the extra spaces between dice to separate them.
Usually, manufacturers mount wafers onto tape to improve their backside support. Once the wafer has been mounted, it’s loaded into a cassette and then into the actual dicing mechanism, which cuts the wafer into individual dice.
The dicing mechanism contains an abrasive blade that it rotates with a spindle at high speeds (usually 30,000–60,000 rpm).
Blades used for this purpose comprise diamond grit embedded into an electroplated nickel matrix. Because these blades are so strong, they easily crush wafers, and any debris that it creates can be removed while the machine works.
The blade moves between active areas of the dice through dedicated lines known as streets. This creates a groove in the substrate material.
Wafer Dicing Techniques
Wafer Scribing
The term “scribing” refers to a specific die singulation technique. This technique uses only one process tool to partially cut through a wafer. Then, a breaking step divides the wafer into individual dice along scribed lines. This separates scribing from the more traditional option of dicing, which involves cutting through a wafer entirely in just one step.
Through Cutting
When wafers are through cut on tape, it’s easy to achieve higher tolerances on the final chip size. The primary drawback of this process is that it can result in some bottom-side chipping. Some manufacturers get around this by wax mounting wafers onto glass to offer more precise cuts.
Wax Mounting
Wax mounting on glass is labor intensive, but doing so often leads to superior quality. Before the process can begin, manufacturers must clean the workpieces, which helps achieve the best possible edge quality. When substrates are wax mounted on glass, the superior bottom-side support results in fewer instances of chipping. Sometimes tape mounting is used for a simpler process.
Wafer Dicing Services at Kadco Ceramics
Dicing work involves quartz, alumina, piezoceramics, glass, and layered combinations of materials. Our work involves not only die singulations on wafers but also cutting grooves and forming surface features.
Our staff uses multiple Disco and K&S dicing machines to meet our clients’ wafer dicing needs. Our certified team of engineers is dedicated to understanding the individual needs of each client—they’ll speak with you about your goals, the tradeoffs you may make to reach them, and any other requirements you’re working with.
If you would like to learn more about Kadco Ceramics’ wafer dicing services, contact us today.